Introduction
Bachy Soletanche has pioneered the diaphragm wall technique in the South-East Asia region and has successfully completed numerous building and infrastructure projects in Hong Kong and Macau.
The diaphragm wall is a method frequently used to provide a permanent support of excavation, build or deep continuous cut-off walls.
This can be used for all types of structures – underground stations, buildings, car parks, tanks, dams – and in all types of soil and rock.
This method is suitable for urban environment, when working close to existing structures though a minimum clearance is required for the thickness of the guide wall. It is particularly suited to excavations carried out below the water table.
Implementation
A diaphragm wall is a reinforced concrete wall that is cast in sections or panels excavated in the ground. The trench, which can reach 90m depth and beyond held open during excavation, and installation of reinforcement and concrete by the use of a supporting slurry.
The diaphragm wall thicknesses are usually: 0.80m; 1.00m; 1.20m; 1.50m; 1.80m.
A mechanical or hydraulic grab or a Hydrofraise® (technology developed by Soletanche Bachy) is used depending on the type of soil encountered.

Our Processes
In general, the construction of a diaphragm wall follows the following steps:
Step 1
The temporary guide walls are constructed in advance and consist of two reinforced-concrete sections each about 30cm thick and 1m deep. The guide-walls have several functions:
- to provide physical confirmation of the location of the wall,
- to guide the excavation tool,
- to provide a reservoir for drilling mud,
- to provide a fixed support for suspension of the reinforcement cages.
Concrete guide walls can be poured flush to existing structures and foundations. This allows to build diaphragm walls very close to nearby constructions.
Step 2
Excavation phase is made of one or several overlapping bites forming a panel, with the help of a support slurry. The properties of this slurry and the length of the excavated panel are adapted to site conditions and presence of structures in the vicinity to guarantee an optimal trench stability at all times.
During the excavation process the soil is progressively replaced by the support slurry, usually made of bentonite. Depending on specific ground conditions, bentonite can be replaced by biodegradable polymers. Other options are possible.
Step 3
When the excavation of a panel is complete, the slurry is treated to reduce the quantity of solids in suspension to a predetermined acceptable level.
Then the reinforcement is placed in the panel. It is made of pre-fabricated cages that are carefully lifted, positioned within the trench and overlapped. The number of cages depends on the depth of the panel.
Step 4
Once the reinforcement cage has been placed, tremie pipes are put in place through the cage till the bottom of the excavated panel. The tremie pipe method prevents the segregation of the concrete, thus ensuring the good quality of the works.
Concrete is then poured from platform level. During this operation, the concrete encapsulates the steel cage and pushes out the support slurry which is pumped away and recycled.
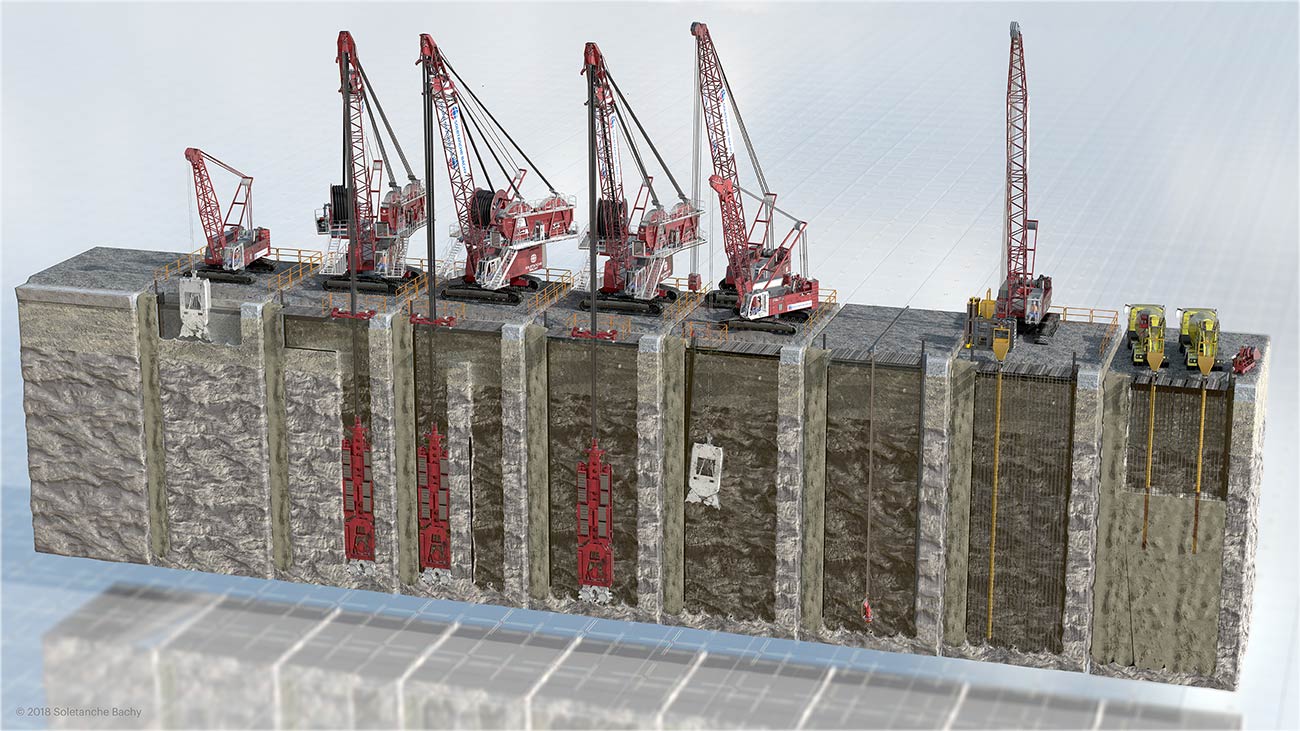